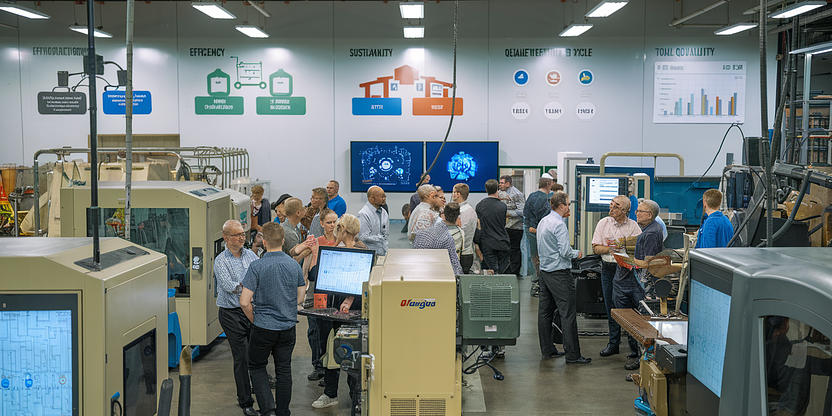
The Complete Checklist for Continuous Improvement in Manufacturing
Mastering Continuous Improvement in Manufacturing
In the fast-paced and competitive world of manufacturing, companies are relentlessly striving for excellence, efficiency, and innovation. Continuous Improvement (CI) is a vital philosophy and set of practices manufacturing companies use to enhance productivity, reduce waste, improve quality, and foster a culture of perpetual growth. These initiatives are paramount to staying competitive in today’s global market.
Adopting a mindset of constant refinement empowers organizations to streamline operations, meet customer expectations more effectively, and ensure long-term success. Drawing from methodologies such as Lean Manufacturing, Six Sigma, and Total Quality Management (TQM), CI encompasses various strategies tailored to an organization's unique needs and challenges.
The Concept of Continuous Improvement
Continuous Improvement is rooted in the belief that there is always scope for improvement, no matter how well a process operates. By systematically eliminating inefficiencies and optimizing processes, manufacturing companies can achieve more with less. CI is not a one-time event but a long-term commitment that involves iterative cycles of planning, execution, evaluation, and refinement.
Important Components of Continuous Improvement in Manufacturing
Employee Involvement: Employees are the backbone of CI efforts. By engaging them in problem-solving and decision-making processes, manufacturers can harness diverse perspectives and ideas for improvement.
Customer Focus: Understanding and anticipating customer needs is crucial. Continuous Improvement should always aim to enhance customer satisfaction by delivering better products and services.
Data-Driven Decision Making: Fact-based decisions leveraging data analytics can improve accuracy and result in more targeted improvement efforts.
Process Standardization: Establishing clear and standardized procedures ensures consistency in operations, reducing errors and variability.
Technology Utilization: Leveraging modern technologies such as IoT, AI, and Machine Learning can dramatically enhance the ability to monitor, analyze, and improve manufacturing processes.
Sustainability: Efficient use of resources reduces environmental impact and often leads to cost savings, aligning CI efforts with sustainability goals.
The Continuous Improvement Cycle
Often visualized as a cycle, Continuous Improvement involves several key steps:
- Identify Opportunities: Continually scrutinize processes to identify areas where performance can be enhanced.
- Plan: Develop actionable plans with specific goals and benchmarks.
- Implement: Execute these plans on a small scale to assess their effectiveness.
- Review: Analyze outcomes to understand what worked and what didn’t.
- Refine: Make necessary adjustments based on observations, and scale up successful strategies.
Practical Checklist for Continuous Improvement in Manufacturing
To aid in rolling out a structured CI program, the following checklist provides a comprehensive guide:
-
Leadership Commitment
- ☐ Ensure top management demonstrates a commitment to CI.
- ☐ Establish a clear vision and objectives related to improvement goals.
-
Training and Development
- ☐ Conduct CI training for all employees.
- ☐ Promote a culture of learning and skill development.
-
Data & Tools
- ☐ Implement data collection tools for measuring performance.
- ☐ Use statistical analysis tools for insightful data interpretation.
-
Process Mapping
- ☐ Document and map out all current processes.
- ☐ Identify bottlenecks and areas for improvement.
-
Employee Engagement
- ☐ Set up a system for employee suggestions and feedback.
- ☐ Recognize and reward contributions to CI.
-
Benchmarking & Metrics
- ☐ Define KPIs to measure improvement progress.
- ☐ Regularly compare performance against industry standards.
-
Implementation Plan
- ☐ Develop a detailed CI implementation roadmap.
- ☐ Set short-term and long-term improvement milestones.
-
Feedback Loops
- ☐ Establish feedback systems to gather input post-implementation.
- ☐ Evaluate feedback to refine processes continuously.
-
Sustainability Initiatives
- ☐ Incorporate eco-friendly practices in improvement plans.
- ☐ Measure resource usage and seek reductions in waste generation.
-
Technology Integration
- ☐ Explore technology solutions for process automation.
- ☐ Ensure technology is aligned with CI objectives.
The Benefits of Continuous Improvement
Adopting continuous improvement processes can lead to several significant benefits such as increased operational efficiency, cost reductions, heightened quality of products, enhanced customer satisfaction, and a motivated workforce that is invested in the organization's success.
Companies that prioritize CI position themselves to better navigate the uncertainties of the modern manufacturing landscape. By iteratively refining processes, they not only improve their bottom line but also enhance their reputation and competitiveness on the global stage.
Conclusion
In conclusion, Continuous Improvement in manufacturing is not an option but a necessity for companies seeking success in today's competitive market. By fostering a culture where every employee is engaged in the pursuit of excellence, leveraging data and technology, and integrating sustainability into their operations, manufacturers can unlock unparalleled growth and innovation.
Armed with this comprehensive checklist and a commitment to ongoing development, organizations can embark on a journey of never-ending enhancement and excellence in manufacturing.