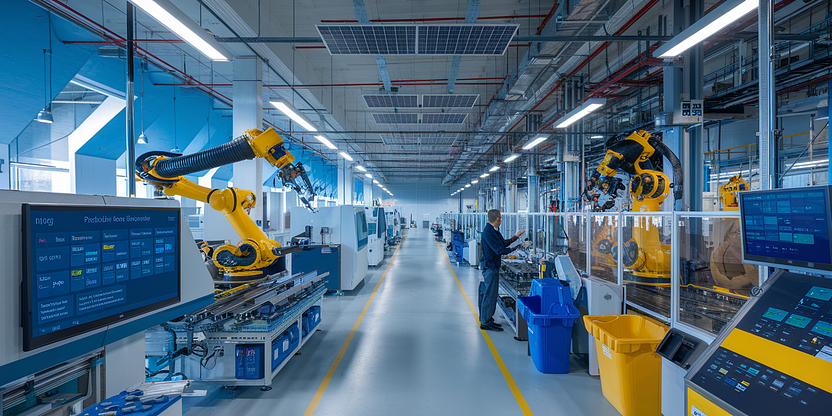
The Complete Checklist for Cost Reduction Strategies in Manufacturing
Cost reduction strategies in manufacturing are crucial for maintaining a competitive edge in the market. They entail a detailed analysis and implementation of various techniques aimed at minimizing production costs while maintaining, or even enhancing, product quality. In this article, we delve into comprehensive strategies across different facets of manufacturing that can significantly lower costs. Along with a detailed checklist, we will explore technological upgrades, process improvements, workforce optimization, supply chain efficiencies, and waste reduction as key areas where manufacturers can focus their efforts.
Technological Upgrades and Automation
Technological advancements in the realm of automation and production equipment can seamlessly pave the way for cost reduction in manufacturing. Investing in robotics and advanced machinery can lead to higher precision and increased production speeds. Furthermore, the adoption of software for predictive maintenance can avert unexpected downtimes, thus reducing maintenance costs. Here are several focal strategies:
- Investment in Robotics: Automate repetitive tasks to increase efficiency and decrease labor costs.
- Predictive Maintenance Software: Reduce machine downtime and costly repairs by forecasting potential breakdowns.
- Digital Twins and Simulation: Use virtual models to improve production planning and identify inefficiencies.
- Internet of Things (IoT): Enhance connectivity and data analysis for smarter decision-making processes.
Process Improvements and Lean Manufacturing
Implementing lean manufacturing processes focuses on maximizing productivity by reducing waste and non-value-added activities. This philosophy encourages continual improvement and aims to create more value with fewer resources. Here’s how you can streamline processes:
- Value Stream Mapping: Visualize and analyze the flow of materials and information to identify bottlenecks.
- 5S Methodology: Organize and standardize the workspace to enhance productivity and safety.
- Kaizen Approach: Encourage small, incremental changes in processes focused on ongoing improvement.
- Just-in-Time (JIT) Production: Reduce inventory costs by aligning production schedules with demand forecasts.
Workforce Optimization
The workforce plays a critical role in cost reduction strategies. Ensuring that employees are well-trained and their skills properly aligned with company goals can lead to significant productivity gains.
- Comprehensive Training Programs: Equip the workforce with skills to handle new technologies and processes.
- Employee Involvement: Foster a participative culture where employees contribute ideas for efficiency improvements.
- Performance Incentives: Encourage higher productivity and lower turnover with performance-based rewards.
- Flexible Work Arrangements: Optimize labor costs by adjusting workforce levels in response to demand fluctuations.
Supply Chain Efficiencies
An optimized supply chain can greatly reduce manufacturing costs by minimizing delays and reducing unnecessary expenditures on logistics. Consider these supply chain strategies:
- Supplier Consolidation: Work with a select group of reliable suppliers to foster stronger relationships and better pricing.
- Inventory Optimization: Use inventory management software to maintain an optimal level of stock.
- Collaborative Planning: Engage in joint forecasting and planning with suppliers to improve supply chain responsiveness.
- Outsourcing Non-Core Activities: Focus on core competencies by outsourcing ancillary operations to specialized companies.
Waste Reduction and Environmental Sustainability
Reducing waste not only cuts costs but also supports sustainable practices that are increasingly valued by today’s consumers. Environmental consciousness can also lead to financial incentives such as tax breaks and subsidies.
- Energy Efficiency: Invest in energy-efficient machinery and lighting to reduce utility bills.
- Recycling and Reuse: Implement recycling systems to minimize waste and reduce raw material costs.
- Waste Audits: Conduct regular audits to identify and eliminate sources of waste.
- Sustainable Packaging: Use biodegradable or recyclable materials to align with sustainability goals and reduce costs.
The Complete Checklist for Cost Reduction Strategies in Manufacturing
Here is a comprehensive checklist summarizing the key strategies for reducing costs in manufacturing that have been discussed:
-
Technological Upgrades
- Implement robotics and automation.
- Utilize predictive maintenance technology.
- Explore digital twin and IoT applications.
-
Process Improvements
- Conduct value stream mapping.
- Apply the 5S methodology.
- Adopt the Kaizen approach.
- Implement Just-in-Time (JIT).
-
Workforce Optimization
- Develop and maintain training programs.
- Encourage employee involvement.
- Implement performance incentive systems.
- Offer flexible work arrangements.
-
Supply Chain Efficiencies
- Consolidate suppliers.
- Optimize inventory levels.
- Engage in collaborative planning.
- Outsource non-core activities.
-
Waste Reduction
- Improve energy efficiency.
- Develop a recycling and reuse program.
- Conduct regular waste audits.
- Use sustainable packaging options.
By adhering to this checklist, manufacturers can strategically initiate and manage cost reduction programs that improve their bottom line while maintaining high-quality production standards. In an ever-evolving manufacturing landscape, these strategies go beyond mere cost-cutting to foster innovation, sustainability, and long-term growth.