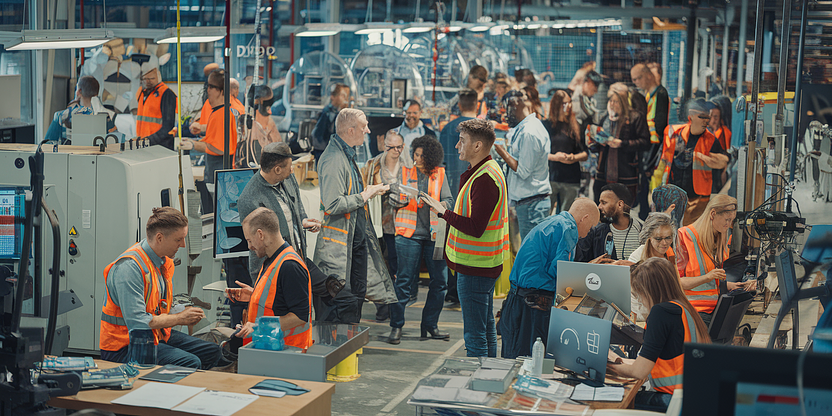
The Complete Checklist for Effective Communication in Manufacturing
Effective communication in manufacturing is essential for ensuring operational efficiency, maintaining safety standards, and fostering a productive work environment. The multifaceted nature of manufacturing processes, which often involve various departments, machines, and personnel, necessitates precise and respectful communication. Miscommunications can lead to costly delays, safety incidents, and a decline in product quality. Thus, developing a comprehensive strategy for effective communication is vital. Below is an exploration of the key components of effective communication within the manufacturing sector, enriched by a detailed checklist to bridge any communication gaps.
The Importance of Effective Communication in Manufacturing
Communication in manufacturing involves a complex network of interactions among workers, engineers, managers, and across departments such as procurement, quality assurance, and logistics. Improved communication can lead to better collaboration, innovation, and faster problem resolution. It also enhances employee morale as clarity reduces frustration and increases job satisfaction.
Challenges in Manufacturing Communication
Diverse Workforces: Manufacturing often employs a mix of skilled labor, engineers, and management, making standardization of communication methods necessary.
Technical Jargon: The use of specialized language and terminology can create barriers if not communicated clearly to all levels.
Shift Work: Different working hours for shifts can result in a breakdown of communication continuity.
Safety Concerns: Critical safety information needs to be communicated precisely and promptly to prevent accidents.
Technology Integration: Adapting to new communication technologies and ensuring that all personnel are adequately trained can be challenging.
Building Blocks of Effective Communication
1. Clear Objectives: Define what each communication seeks to achieve. Whether it’s daily operational goals or emergency alerts, clarity of purpose is crucial.
2. Standard Operating Procedures (SOPs): Develop SOPs for communication to ensure consistency and reliability in the transmission of information.
3. Training and Development: Regular training sessions on communication skills and technology use can enhance clarity and reduce misunderstandings.
4. Feedback Mechanisms: Establish channels where employees feel comfortable providing feedback. Encourage active listening and responsive actions based on this feedback.
5. Multichannel Communication: Utilize a range of communication channels, from face-to-face meetings to digital platforms, to reach all stakeholders effectively.
6. Documentation: Keep meticulous records of communications to ensure accuracy and accountability.
7. Cultural Sensitivity: Acknowledge the multicultural nature of many workplaces and adapt communication practices accordingly.
The Actual Checklist for Effective Communication in Manufacturing
Here is a practical checklist to ensure comprehensive communication:
-
Conduct a Communication Audit:
- Identify current communication channels and their effectiveness.
- Evaluate the gaps and redundancies.
-
Establish Clear Channels:
- Determine preferred modes of communication for various scenarios (e.g., meetings, emails, bulletin boards, intercom systems).
-
Review and Update SOPs:
- Regularly revisit communication protocols to ensure relevance with current manufacturing processes.
-
Implement Training Programs:
- Schedule regular workshops to enhance communication skills and technology usage.
-
Encourage Immediate Feedback:
- Install mechanisms such as suggestion boxes or digital platforms for employee input.
-
Leverage Technology:
- Utilize tools such as project management software, instant messaging, and video conferencing for improved communication.
-
Designate Communication Custodians:
- Assign personnel responsible for ensuring that communication guidelines are followed and effective.
-
Conduct Regular Meetings:
- Host daily briefings and monthly reviews to facilitate continuous dialogue between teams.
-
Evaluate Safety Communication:
- Ensure that safety protocols and updates are communicated immediately and clearly to avoid hazards.
-
Facilitate Cross-Department Interactions:
- Organize interdepartmental coordination meetings to ensure alignment of goals.
Implementing the Checklist: A Step-by-Step Guide
Step 1: Initial Assessment
Begin by thoroughly assessing your current communication strategies using the checklist. Recognize areas that require improvement or realignment.
Step 2: Customize Communication Methods
Develop methods tailored to your specific manufacturing environment, considering aspects like workforce diversity and technological capacity.
Step 3: Training and Engagement
Initiate training programs focused on communication skills, extending beyond traditional modes to include online platforms and apps.
Step 4: Monitor and Review
Regularly monitor the effectiveness of communication practices and solicit feedback. Adjust strategies as needed to maintain optimal communication.
Step 5: Continual Improvement
Commit to a cycle of continuous improvement by staying updated with the latest technologies and adjusting your communication strategy accordingly.
Conclusion
Effective communication in manufacturing is a critical component that binds various facets of operational success. By leveraging a robust and practical checklist, manufacturing entities can ensure clarity, enhance collaboration, and maintain safety across all levels. This strategic approach to communication not only resolves current inefficiencies but also positions the manufacturing plant to embrace future innovations and challenges with greater confidence and agility.