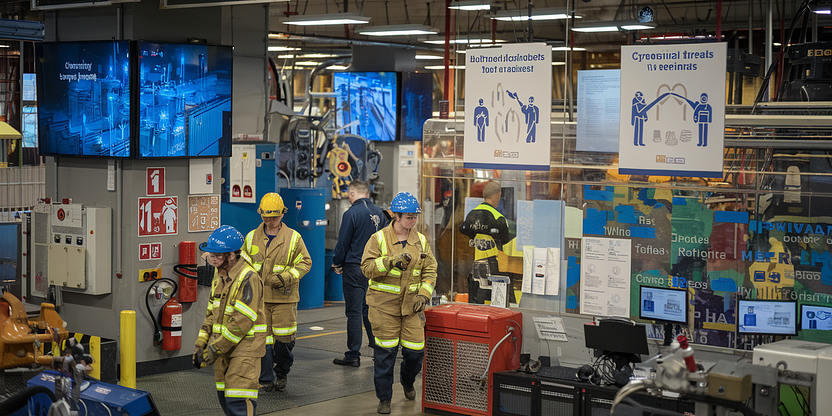
The Complete Checklist for Emergency Preparedness in Manufacturing
Navigating the Unexpected: An In-Depth Guide to Emergency Preparedness in Manufacturing
In the ever-evolving arena of manufacturing, ensuring safety and operational continuity is paramount. Manufacturing environments are fraught with potential hazards—from mechanical malfunctions and environmental disasters to cyber threats. Emergency preparedness is not merely an option but a necessity that can mean the difference between chaos and continuity.
Proper preparation involves a comprehensive strategy that safeguards resources, protects employees, and ensures the continuation of critical operations. Building such a strategy requires understanding the potential threats, creating a robust plan, and implementing preventive measures. This article provides you with a complete checklist to bolster emergency preparedness in your manufacturing facility.
Understanding the Risks
Before diving into the checklist, it’s important to understand the range of emergencies that can impact a manufacturing plant. These could include:
- Natural Disasters: Earthquakes, floods, hurricanes, and other natural phenomena can have devastating effects on manufacturing operations.
- Industrial Accidents: Equipment failures, chemical spills, or fires can result in significant harm and damage.
- Cybersecurity Threats: With increasing reliance on technology, cyber-attacks pose a considerable risk.
- Pandemics and Public Health Crises: These have highlighted the need for operational adaptability.
- Supply Chain Disruptions: Strikes, supplier failures, or transport issues can interrupt the flow of materials and goods.
Building the Framework: The Checklist for Emergency Preparedness
Creating a comprehensive emergency preparedness plan involves several steps. Here is a detailed checklist to guide your efforts:
1. Risk Assessment and Analysis - Conduct a thorough risk assessment to understand potential threats specific to your location and operations. - Prioritize risks based on likelihood and impact.
2. Development of Emergency Plan - Develop an emergency response plan tailored to identified risks. - Ensure the plan includes procedures for evacuation, communication, resource allocation, and continuity strategies. - Designate roles and responsibilities for emergency response teams.
3. Communication Strategies - Establish a robust internal and external communication plan. - Set up a notification system to alert employees and stakeholders. - Develop contingency plans for loss of communications systems.
4. Training and Drills - Conduct regular training sessions for employees on emergency procedures. - Organize regular drills to ensure readiness and refine procedures. - Train personnel on the use of emergency equipment and first aid.
5. Review and Update Plans - Schedule regular reviews and updates of the emergency preparedness plan. - Incorporate feedback and new developments into the plan. - Ensure compliance with any legal or industry-specific requirements.
6. Equipment and Resources Management - Maintain and routinely check emergency equipment like fire extinguishers, alarms, and protective gear. - Ensure access to emergency kits and supplies, including first aid, food, and water. - Have backup systems for essential utilities and computer systems.
7. Cybersecurity Measures - Implement robust cybersecurity protocols to safeguard digital assets. - Conduct regular software updates and vulnerability assessments. - Educate employees on best practices for data protection and threat recognition.
8. Collaboration with Authorities and Community - Establish connections with local emergency services and authorities. - Develop strategies for information-sharing with community stakeholders. - Participate in mutual aid agreements with neighboring businesses.
Implementation and Review
Implementing an emergency preparedness plan requires commitment across the organization. It should be a collaborative effort involving all stakeholders from executives to entry-level employees. Regularly testing and updating the plan is critical, as this ensures that it remains relevant and effective.
The Human Element
No plan can succeed without considering the human element. Employees need to be not only informed but engaged in the preparedness process. This entails fostering a culture of safety and responsibility. Encourage employee feedback to continuously improve practices and build a resilient workforce.
Conclusion
The unpredictability of the world demands that manufacturing plants be prepared for unforeseen events. A well-structured emergency preparedness plan reduces risks, enhances safety, and ensures operational continuity. Using the checklist provided, manufacturing facilities can approach preparedness with confidence, safeguarding both human and material resources. Preemptive action doesn’t just protect against disaster; it fortifies the very foundation upon which successful manufacturing is built.