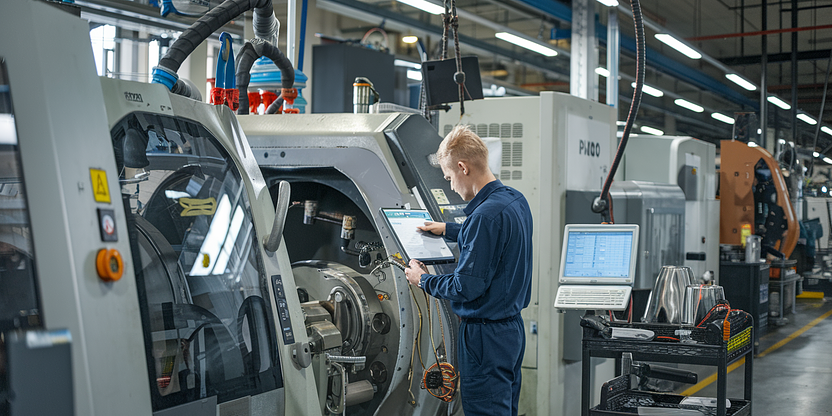
The Complete Checklist for Equipment Maintenance in Manufacturing
Ensuring Efficiency: A Comprehensive Guide to Equipment Maintenance in Manufacturing
In the fast-paced world of manufacturing, equipment reliability and efficiency are paramount. Keeping machinery in optimal working condition is critical not only for maintaining production schedules but also for ensuring product quality and workplace safety. Implementing a well-structured maintenance program can prevent unexpected breakdowns, reduce downtime, and extend the life of equipment. This article provides an extensive guide on best practices for equipment maintenance, supplemented by a practical checklist to streamline your maintenance processes.
Understanding Equipment Maintenance
Equipment maintenance involves a combination of various practices aimed at ensuring machinery runs smoothly, efficiently, and without unexpected interruptions. The core types of maintenance include:
Preventive Maintenance (PM): Scheduled, routine maintenance to prevent equipment failure. It includes inspections, adjustments, cleaning, lubrication, and part replacements.
Predictive Maintenance (PdM): Uses data analytics and tools to predict equipment failures based on condition-monitoring.
Corrective Maintenance (CM): Reactive repairs required to fix equipment failures after they occur.
Condition-Based Maintenance (CBM): Maintenance when specific indicators show that equipment is deteriorating or is about to fail.
Benefits of a Robust Maintenance Program
- Increased Equipment Lifespan: Regular maintenance can extend the operational life of equipment, delaying costly replacements.
- Enhanced Efficiency and Productivity: Well-maintained equipment performs optimally, reducing energy use and increasing output.
- Reduced Downtime and Costs: Scheduled maintenance prevents costly unexpected breakdowns, saving money on repairs and reducing lost production time.
- Improved Safety: Regular inspections and maintenance reduce the risk of accidents caused by equipment failures.
Developing an Effective Maintenance Strategy
Inventory and Audit: Catalog all equipment, noting their specifications, operational history, and maintenance requirements. Audits help evaluate the current health and performance levels.
Prioritization: Classify equipment based on criticality to operations. Focus on the most essential machinery to minimize disruption risks.
Training and Skills Development: Ensure that personnel are trained and knowledgeable about maintenance procedures and how to handle equipment safely.
Integration of Technology (IoT and AI): Use smart sensors and data analytics to monitor equipment performance and predict failures.
Scheduled Checks: Establish a routine schedule based on the manufacturer’s recommendations and historical data for conducting maintenance.
Implementing the Checklist
Below is a detailed checklist for maintaining equipment in a manufacturing setting:
Equipment Maintenance Checklist
-
Documentation:
- [ ] Ensure all manuals and repair histories are up-to-date.
- [ ] Verify that each machine has a logbook for recording maintenance activities.
-
Routine Inspections:
- [ ] Conduct visual inspections for signs of wear or damage.
- [ ] Check for any unusual noises or vibrations.
- [ ] Inspect safety features and guards for compliance.
-
Lubrication and Cleaning:
- [ ] Apply appropriate lubricants to reduce friction and wear.
- [ ] Clean machinery to prevent dust buildup, especially in moving parts.
-
Calibration:
- [ ] Calibrate instruments and sensors to ensure accuracy.
- [ ] Adjust machine settings to optimal performance specifications.
-
Part Replacements and Repairs:
- [ ] Replace worn or damaged components as per maintenance schedule.
- [ ] Assess and perform necessary repairs on detecting faults.
-
Electrical and Mechanical Systems Check:
- [ ] Inspect wiring and electrical systems for safety hazards.
- [ ] Ensure all belts, bolts, and mechanical components are secure.
-
Software and Control Systems:
- [ ] Update firmware and software to latest versions for efficiency.
- [ ] Test and verify control system settings and alarms.
-
Safety Compliance:
- [ ] Check that all safety signage and instructions are visible.
- [ ] Confirm that emergency stops and safety interlocks are functioning.
-
Reporting:
- [ ] Document every maintenance check and corrective action taken.
- [ ] Compile reports on equipment performance and maintenance outcomes.
Continuous Improvement and Feedback Loop
After implementing a robust maintenance plan, it is crucial to regularly review its effectiveness and adapt based on feedback and technological advancements. Encouraging worker feedback and staying informed about industry trends can help in refining maintenance practices over time. Establish regular meetings to discuss equipment condition, review the checklist application, and promote a culture of continuous improvement.
Conclusion
A meticulous approach to equipment maintenance not only protects investments in machinery but also secures a competitive edge in manufacturing by ensuring seamless operations. By integrating the strategies and checklist outlined in this guide, manufacturers can safeguard against disruptions, optimize resource allocation, and achieve long-term business success. Through consistency and commitment to maintenance, organizations can unlock greater productivity and maintain high standards of safety and quality.