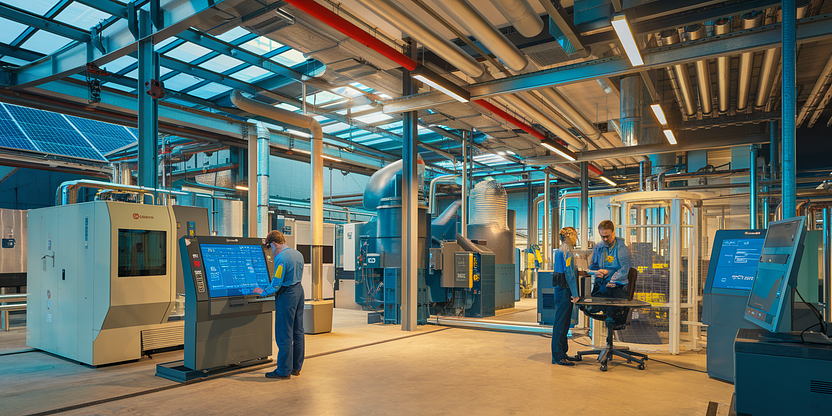
The Complete Checklist for Industrial Energy Optimization
Maximizing Efficiency: The Complete Guide to Industrial Energy Optimization
In an era where sustainability and cost-effectiveness are at the forefront of industrial priorities, energy optimization stands tall as a critical component for modern enterprises. As industries continue to expand, so do their energy demands, impacting both the environment and the bottom line. This article explores the various dimensions of industrial energy optimization, highlighting strategies, technologies, benefits, and a comprehensive checklist to guide your efforts in achieving energy efficiency.
Understanding Industrial Energy Optimization
Energy optimization in industrial settings involves adopting strategies and employing technologies that minimize energy consumption while maintaining or enhancing productivity. It is a multifaceted approach that includes assessing energy use, identifying inefficiencies, implementing solutions, and maintaining them for long-term success. The primary goals are reducing operational costs, minimizing carbon footprints, and complying with environmental regulations.
Key Components of Energy Optimization
Energy Audits: These are comprehensive reviews of energy usage patterns in a facility. An audit identifies areas where energy can be used more efficiently, saving money and reducing emissions.
Energy Management Systems (EMS): Advanced technologies that track and manage energy use in real-time. By integrating EMS with industrial operations, companies can cut unnecessary energy consumption and quickly identify and correct inefficiencies.
Equipment Upgrades: Often, outdated machinery consumes more energy than newer models. Investing in modern equipment with high energy efficiency ratings can lead to significant savings.
Behavioral Changes: Educating employees about energy conservation and encouraging changes in behavior can lead to notable drops in energy use.
Renewable Energy Solutions: Utilizing renewable energy sources such as solar, wind, or biomass can significantly reduce reliance on non-renewable energy, reducing carbon footprints.
Process Optimization: Streamlining workflows to eliminate waste can lead to reduced energy consumption. Lean manufacturing techniques are commonly employed for this purpose.
Heat Recovery Systems: Capturing and reusing waste heat from industrial processes can improve energy efficiency and reduce costs.
Benefits of Energy Optimization
- Cost Savings: Lower energy bills result in direct financial benefits, improving profit margins.
- Environmental Impact: Reduced energy consumption lowers greenhouse gas emissions, helping combat climate change.
- Compliance and Reputation: Aligning with environmental regulations enhances a company’s reputation and avoids potential penalties for non-compliance.
- Enhanced Reliability: Energy-efficient systems tend to have fewer breakdowns, reducing downtime and maintenance costs.
Checklist for Industrial Energy Optimization
For effective energy optimization, industries should follow this detailed checklist:
-
Conduct a Comprehensive Energy Audit:
- Analyze historical energy usage data.
- Identify peak consumption times.
- Pinpoint inefficient processes and equipment.
-
Implement an Energy Management System (EMS):
- Choose an EMS that suits your industry and facility size.
- Integrate EMS with existing systems for seamless operation.
- Train staff on EMS utilization and benefits.
-
Upgrade Equipment:
- Prioritize high energy-consuming machinery for upgrades.
- Consider solutions like Variable Frequency Drives (VFDs) for electric motors.
- Evaluate the benefits of automation in reducing energy use.
-
Enhance Facility Insulation and Ventilation:
- Inspect and repair any insulation breaches.
- Ensure ventilation systems operate efficiently, using advanced technology like energy recovery ventilators (ERVs).
-
Adopt Renewable Energy Sources:
- Assess feasibility of solar, wind, or other renewable installations.
- Explore government incentives or rebates for renewable projects.
- Monitor performance and optimize placement and maintenance.
-
Optimize Production Processes:
- Implement Lean manufacturing principles to eliminate waste.
- Regularly review and refine processes for better energy performance.
- Utilize energy-efficient scheduling based on peak and off-peak hours.
-
Engage Employees in Energy-Saving Initiatives:
- Conduct training sessions on energy conservation.
- Create incentive programs for energy-saving ideas and practices.
- Regularly communicate sustainability goals and progress.
-
Install Heat Recovery Systems:
- Conduct feasibility studies for waste heat recovery.
- Choose systems that align with production processes.
- Monitor and maintain system performance.
-
Continuously Monitor and Evaluate:
- Use data analytics to track energy usage.
- Regularly meet to discuss findings and implement corrective actions.
- Adjust the energy optimization strategy as necessary.
Conclusion
Industrial energy optimization is not a one-time project but an ongoing commitment to efficiency and sustainability. By following the comprehensive checklist and employing the best practices mentioned above, industries can achieve their energy goals, resulting in substantial economic and environmental benefits. Energy optimization sets a strong foundation for industries striving to be competitive, sustainable, and responsible in today’s energy-conscious world.