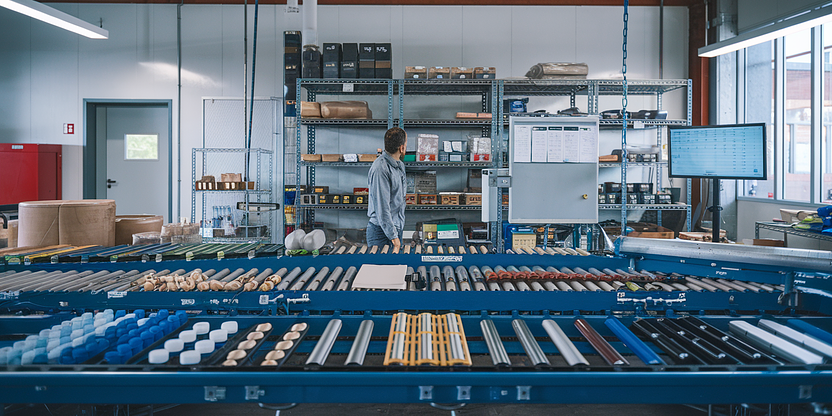
The Complete Checklist for Inventory Management in Manufacturing
Optimizing Inventory Management in Manufacturing
Inventory management is a crucial function in the manufacturing sector, directly influencing production efficiency, cost management, and customer satisfaction. Effective inventory control ensures that a company can meet customer demands promptly while minimizing excess stock and associated holding costs. As such, having a well-structured checklist for inventory management can help manufacturers streamline operations, improve accuracy, and bolster profitability. This guide offers a comprehensive blueprint for mastering inventory management in manufacturing settings.
Understanding Inventory Management in Manufacturing
The essence of inventory management lies in maintaining the right balance between supply and demand. In manufacturing, this typically involves the oversight of raw materials, work-in-progress (WIP) items, and finished goods. Proper inventory management strategies can lead to reduced operating costs, increased cash flow, and enhanced customer satisfaction.
Key components of inventory management include:
- Demand Forecasting: Predicting customer demand to ensure adequate stock levels without overproducing or underproducing.
- Stock Categorization: Segmenting inventory into categories such as critical items, high-value items, and frequently used items to focus on what’s most crucial.
- Lead Time Management: Understanding and managing the time between when an order is placed and when it is received and ready for use.
- Cycle Counting: Regular auditing of inventory to maintain accurate stock levels and identify discrepancies.
- Reorder Points: Setting thresholds that trigger restocking of inventory to prevent stockouts or overstocking.
- Safety Stock Maintenance: Ensuring a buffer stock to protect against unexpected increases in demand or supply delays.
Benefits of Effective Inventory Management
- Cost Savings: Reducing excess stock reduces holding costs, such as storage and insurance expenses.
- Operational Efficiency: Properly managed inventory minimizes production delays by ensuring materials are available when needed.
- Improved Cash Flow: By lowering inventory costs, manufacturers have more capital available for other investments.
- Customer Satisfaction: Meeting delivery deadlines and order fulfillment reinforces trust and improves customer relationships.
Creating the Complete Checklist for Inventory Management
Implementing a comprehensive inventory management checklist is vital for maintaining system efficiency and reliability. Below is a detailed checklist to enhance inventory strategies in manufacturing:
Inventory Management Checklist
-
Analyze Demand and Consumption Patterns
- Implement software tools for demand forecasting.
- Regularly review historical sales and usage data.
- Adjust forecasts based on market trends and customer feedback.
-
Develop a Stock Categorization System
- Classify inventory into A, B, C categories (e.g., high, medium, low importance).
- Prioritize critical and fast-moving items for regular review.
- Apply different management techniques based on categorization.
-
Optimize On-hand Inventory Levels
- Establish minimum and maximum stock levels for each item.
- Use mathematical models like Economic Order Quantity (EOQ) for optimizing order sizes.
- Regularly review and adjust safety stock levels.
-
Enhance Supplier Relationships
- Maintain regular communication with suppliers.
- Develop contingency plans for supplier interruptions.
- Evaluate supplier performance and consider diversification to minimize risks.
-
Implement Technological Solutions
- Deploy inventory management software for real-time tracking.
- Use barcode or RFID technology to automate stocktaking processes.
- Integrate systems with ERP platforms for seamless data flow and analysis.
-
Conduct Regular Inventory Audits
- Schedule cycle counts to regularly verify inventory accuracy.
- Rectify discrepancies between system records and physical stocks.
- Review audit results to identify areas for process improvement.
-
Ensure Continuous Process Improvement
- Encourage feedback from stakeholders involved in inventory processes.
- Conduct regular training for staff on inventory management best practices.
- Monitor key performance indicators (KPIs) such as inventory turnover rates.
-
Review and Refine Inventory Policies
- Establish clear inventory management policies and procedures.
- Regularly review and update policies to reflect changes in manufacturing practices.
- Communicate policies effectively to all involved personnel.
By adhering to this checklist, manufacturers can ensure effective inventory management, leading to smoother operations and a healthier bottom line. Emphasizing continuous improvement and leveraging technology can provide competitive advantages, positioning companies to better meet the dynamic needs of their markets. Effective inventory management is not just about maintaining stock levels—it's about creating a robust framework that supports business agility and growth.