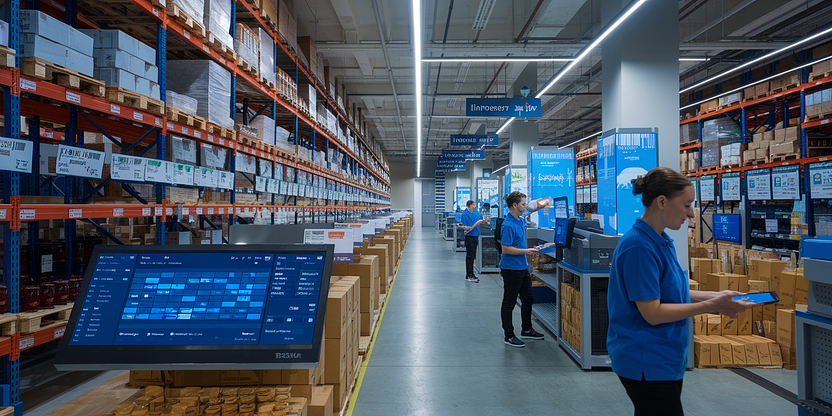
The Complete Checklist for Inventory Management in Retail
Optimizing Retail Success: Navigating Inventory Management
Inventory management is undeniably one of the most crucial aspects of running a successful retail business. At its core, it involves overseeing the precise flow of goods from manufacturers to warehouses and from these storage spaces to the final point of sale. Efficient inventory management ensures that a retail business can meet customer demand without overstocking or stockouts, both of which can be detrimental to the bottom line. Let's explore the key components of successful inventory management in retail, complete with a comprehensive checklist to streamline operations.
Understanding the Basics of Inventory Management
1. Inventory Control: Inventory control involves maintaining optimal inventory levels. By analyzing data regularly, retailers can identify trends and adjust stock levels accordingly. This reduces waste and increases profitability by ensuring that the right products are available at the right time.
2. Stock Classification: Implementing an inventory classification system, such as ABC analysis, helps categorize inventory based on priority. Class A items, for instance, are high-value products with a low sales frequency, whereas Class C items may be low-value with high sales frequency.
3. Demand Forecasting: By utilizing historical sales data, seasonal trends, and market analysis, retailers can predict customer demand more accurately. Advanced demand forecasting software can significantly enhance the accuracy of these predictions, reducing the risk of stockouts or overstocking.
4. Inventory Turnover Ratio: The turnover ratio indicates how often inventory is sold and replaced over a period. Keeping an eye on this metric can help retailers understand how well their products are performing and whether adjustments in purchasing strategy are necessary.
The Role of Technology in Inventory Management
1. Point of Sale (POS) Systems: Modern POS systems automate sales tracking and inventory updates in real-time. This integration allows for seamless management of stock levels and provides valuable sales data for better decision-making.
2. Inventory Management Software: Comprehensive inventory management solutions offer features like automated reorder points, multi-location support, and detailed reporting tools. Such software helps in reducing human error and improving overall efficiency.
3. Radio Frequency Identification (RFID): Implementing RFID technology provides real-time tracking of inventory, minimizes errors, and reduces the labor involved in manual stock takes.
Reducing the Risk of Stockouts and Overstocks
1. Safety Stock: Maintaining a buffer of safety stock can prevent stockouts due to unexpected demand spikes. Calculating an appropriate amount of safety stock involves analyzing historical demand data and adjusting for market variability.
2. Lead Time Optimization: Reducing the lead time from order placement to delivery can minimize the need for excess inventory. Building strong relationships with suppliers can aid in negotiating better lead times.
3. Vendor Managed Inventory (VMI): Employing VMI strategies allows suppliers to manage the inventory levels of their products within a retailer’s system, ensuring a more balanced stock without direct involvement from the retailer.
Implementing Cycle Counting
Regular cycle counting, where a subset of inventory is counted on a rotating schedule, ensures ongoing accuracy in inventory records. It’s a more effective and less disruptive method than occasional end-of-year counts.
A Complete Checklist for Inventory Management Success
Here is a consolidated checklist to help retail businesses manage inventory effectively:
-
Organization and Layout:
- Ensure warehouses and stock rooms are organized.
- Designate specific storage areas for different product categories.
- Label products clearly.
-
Inventory Analysis:
- Conduct regular stock counts.
- Implement ABC classification for inventory.
- Review and analyze sales data periodically.
-
Technology Utilization:
- Use modern POS systems integrated with inventory management software.
- Consider RFID for increased accuracy.
- Evaluate and upgrade software as needed.
-
Demand Forecasting:
- Analyze historical sales data.
- Adjust forecasts for seasonality and trends.
- Utilize advanced forecasting tools and software.
-
Supplier Relationship Management:
- Maintain strong communication with suppliers.
- Negotiate favorable terms and lead times.
- Explore VMI options.
-
Risk Management:
- Calculate and maintain safety stock levels.
- Monitor inventory turnover ratios.
- Develop contingency plans for unexpected demand spikes.
-
Continuous Improvement:
- Regularly re-evaluate inventory processes.
- Stay updated with the latest technology and industry trends.
- Encourage staff training and development.
Conclusion
Efficient inventory management in retail is pivotal to business success. It involves a careful balance of maintaining inventory levels, utilizing technology, understanding market demand, and building solid supplier relationships. By following the comprehensive checklist and insights outlined above, retailers can optimize their inventory management processes, enhancing customer satisfaction while improving profitability. In this fast-paced retail landscape, staying on top of inventory management is not just an operational need but a strategic advantage.