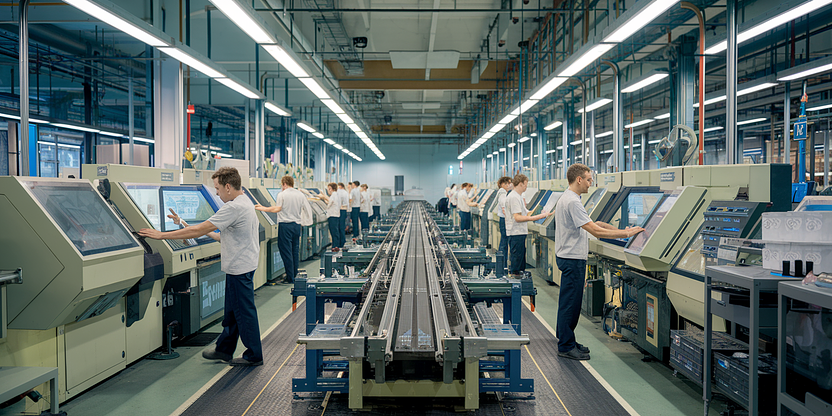
The Complete Checklist for Lean Manufacturing
The Ultimate Guide to Lean Manufacturing
In today’s fast-paced industrial landscape, maintaining efficiency, reducing waste, and adapting to changes swiftly are paramount for any company wishing to maintain a competitive edge. Lean manufacturing emerges as a pivotal methodology that organizations can adopt to achieve operational excellence and cost reduction. Originally developed by Toyota, this systematic approach focuses on streamlining production processes while maximizing value to the customer with minimal resources. Here’s an in-depth dive into lean manufacturing and a comprehensive checklist to implement and sustain it in your operations.
Understanding Lean Manufacturing
Lean manufacturing is more than just a set of tools or practices; it's a philosophy centered on the idea of eliminating waste and optimizing processes. It involves understanding customer value and continuously improving processes to enhance production speed and product quality while decreasing costs and waste.
Core Principles
- Value Identification: Determine what your customers perceive as value, and focus on those activities.
- Value Stream Mapping: Illustrate the flow of materials and information needed to bring a product to the customer, identifying areas of waste.
- Flow Creation: Ensure that work processes are smooth and uninterrupted.
- Pull Production: Produce only what is needed by the customer to reduce excess inventory that ties up capital.
- Perfection Pursuit: Foster a culture of continuous improvement ("Kaizen") where everyone regularly seeks out ways to increase efficiency and reduce waste.
Types of Waste
Lean manufacturing seeks to eliminate the following types of waste, often remembered by the acronym "TIMWOOD":
- Transportation: Unnecessary movement of products and materials.
- Inventory: Excess products and materials not being processed.
- Motion: Unnecessary movement of people or equipment.
- Waiting: Idle time created when materials, information, people, or equipment is not ready.
- Overproduction: Making more than the demand.
- Over-processing: More work or higher-quality work than is required.
- Defects: Efforts caused by rework, scrap, and incorrect information.
Advantages of Lean Manufacturing
Lean manufacturing provides numerous benefits, including:
- Increased Efficiency: Streamlined processes result in faster production times.
- Cost Reduction: Minimizing waste leads to reduced operational costs.
- Improved Quality: Regular assessment and enhancement of processes improve product quality.
- Customer Satisfaction: Meeting customer needs more accurately yields higher satisfaction rates.
- Employee Satisfaction: Empowering employees to identify and solve problems boosts morale.
Implementation Checklist for Lean Manufacturing
Successfully integrating lean manufacturing involves a strategic approach and a robust framework. Here’s a complete checklist to guide your implementation process:
Preparation Phase
-
Conduct an Initial Assessment
- Evaluate current processes and identify existing waste.
-
Secure Executive Commitment
- Gain buy-in from leadership to ensure they understand lean principles and support changes.
-
Assemble a Lean Team
- Form a cross-functional team dedicated to lean initiatives.
-
Set Goals and Objectives
- Define clear, measurable, and achievable goals for your lean journey.
Planning Phase
-
Train Employees
- Conduct workshops to educate employees on lean principles and practices.
-
Create Value Stream Maps
- Document and analyze current processes to identify waste.
-
Develop an Action Plan
- Prioritize areas for improvement and outline steps to address them.
Implementation Phase
-
Implement 5S Method
- Sort, Set in order, Shine, Standardize, and Sustain to maintain organized workspaces.
-
Initiate Kaizen Events
- Conduct focused, short-term projects with targeted improvements.
-
Introduce Key Lean Tools
- Consider tools like Kanban, JIT (Just-In-Time), and Poka-Yoke.
-
Foster Communication & Collaboration
- Encourage open communication and feedback among team members.
Evaluation Phase
-
Measure Progress Regularly
- Use KPIs to track improvements and determine the effectiveness of implemented changes.
-
Acknowledge & Reward Success
- Recognize teams and individuals who contribute to lean success.
-
Reassess and Adjust Goals
- Align goals according to evaluations of progress and industry changes.
Sustainment Phase
-
Cultivate a Lean Culture
- Embed lean principles into the company culture for long-term success.
-
Commit to Continuous Improvement
- Regularly revisit and refine processes to sustain lean practices.
Challenges in Lean Manufacturing
Implementing lean manufacturing is not without challenges. Resistance to change, insufficient training, lack of management support, and difficulty in sustaining lean culture can hinder progress. It’s essential to address these hurdles by fostering a transparent, continuous improvement-focused environment.
Conclusion
Embracing lean manufacturing requires commitment and strategic planning but offers substantial rewards through increased efficiency, quality, and profitability. By following the detailed checklist and fostering a culture that embraces continuous improvement, organizations can achieve and sustain the benefits of lean manufacturing. As global competition intensifies, adopting lean practices not only sharpens your competitive edge but also paves the way for innovative growth and customer satisfaction.