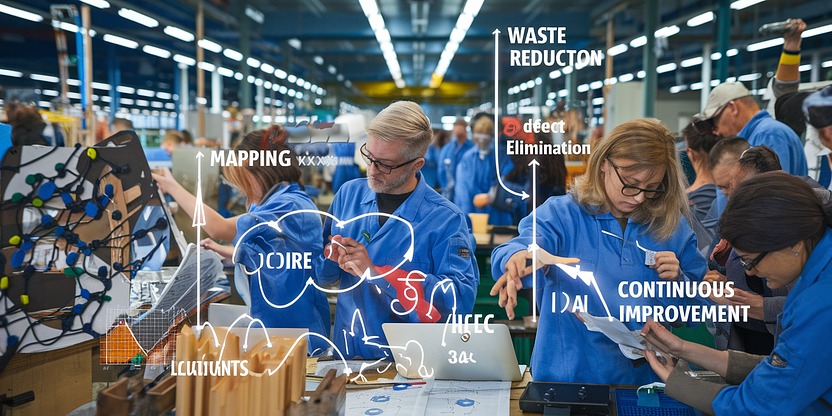
The Complete Checklist for Lean Six Sigma in Manufacturing
Mastering Lean Six Sigma in Manufacturing: A Comprehensive Guide and Checklist
Lean Six Sigma is a powerful methodological approach that combines the lean manufacturing principles aimed at minimizing waste with Six Sigma’s focus on reducing variation and improving process quality. The integration of these two methodologies creates a structured approach to solving problems and improving business processes that is particularly beneficial in the manufacturing sector. This article provides a detailed look at Lean Six Sigma for manufacturing and offers a comprehensive checklist to ensure successful implementation.
Understanding Lean Six Sigma
Lean Six Sigma is built on two foundations: Lean, which emphasizes reducing waste and improving process flow, and Six Sigma, which aims to reduce defects and variability. Together, these methodologies provide a framework that can improve efficiency and quality in manufacturing.
Key Concepts:
- Waste Reduction: Identifying and eliminating non-value-adding activities.
- Defect Reduction: Utilizing data-driven techniques to reduce process variation and defects.
- Continuous Improvement: Adopting a mindset of ongoing process evaluation and improvement.
- Value Stream Mapping: Visualizing entire workflows to detect inefficiencies and areas for improvement.
- 5S Methodology: Streamlining operations by sorting, setting in order, shining, standardizing, and sustaining.
The Lean Six Sigma Process
Lean Six Sigma follows a structured problem-solving process known as DMAIC: Define, Measure, Analyze, Improve, and Control.
- Define: Identify the problem and outline the project goals.
- Measure: Collect life cycle data and determine current performance baselines.
- Analyze: Investigate data to identify root causes of defects and inefficiencies.
- Improve: Implement solutions to address root causes and optimize processes.
- Control: Sustain improvements with monitoring and control mechanisms.
Implementing Lean Six Sigma in Manufacturing
To successfully implement Lean Six Sigma in manufacturing environments, organizations should consider the following elements:
- Strong Leadership Commitment: Leaders must be dedicated to supporting Lean Six Sigma initiatives with resources and a clear vision.
- Employee Engagement: Empower employees by involving them in decision-making and problem-solving processes.
- Training and Resources: Equip staff with the necessary knowledge and tools through workshops and training programs.
- Data-Driven Approach: Leverage data for informed decision-making at every stage of the DMAIC process.
The Complete Lean Six Sigma Checklist
To assist with the implementation of Lean Six Sigma, the following checklist will serve as a step-by-step guide to ensure all vital areas are covered.
Lean Six Sigma Implementation Checklist:
-
Initial Assessment
- [ ] Conduct a baseline assessment to understand current process performance.
- [ ] Identify key value streams and processes.
- [ ] Quantify the impact of waste and variability on performance.
-
Project Planning
- [ ] Define clear, measurable goals aligned with business objectives.
- [ ] Select and prioritize projects based on potential impact and feasibility.
- [ ] Establish a project timeline and resource requirements.
-
Training and Development
- [ ] Train key personnel in Lean Six Sigma methodologies (e.g., Green Belts, Black Belts).
- [ ] Develop cross-functional teams for project execution.
-
Execution of Projects
- [ ] Implement DMAIC methodology for each project.
- [ ] Utilize tools such as Value Stream Mapping, 5 Whys, Fishbone Diagrams, and SIPOC.
- [ ] Regularly review project status and performance metrics.
-
Performance Measurement and Analysis
- [ ] Collect qualitative and quantitative data throughout the process.
- [ ] Analyze data to confirm root causes of inefficiencies and defects.
- [ ] Validate improvements with both short-term and long-term metrics.
-
Sustainability and Control
- [ ] Develop control plans to ensure process maintenance.
- [ ] Implement ongoing monitoring systems for continuous feedback.
- [ ] Foster a culture of continuous improvement among teams.
-
Review and Feedback
- [ ] Conduct final reviews of completed projects.
- [ ] Gather and analyze feedback from stakeholders.
- [ ] Document lessons learned and best practices for future projects.
Case Studies and Benefits
Various manufacturing companies have reported significant improvements as a result of integrating Lean Six Sigma. For instance, a multinational automotive manufacturer used Lean Six Sigma to reduce process defects by 50% and increase production efficiency by 25%, illustrating the powerful potential of this methodology to drive change.
The benefits of Lean Six Sigma in manufacturing are wide-ranging, including higher customer satisfaction, cost efficiencies, innovation, and improved operational performance.
Conclusion
Lean Six Sigma is more than a process improvement tool—it’s a paradigm shift that transforms both culture and operations. By following the structured approach and utilizing the comprehensive checklist provided, manufacturing companies can significantly enhance their competitiveness and operational excellence. Whether you’re at the beginning of your Lean Six Sigma journey or seeking to refine your current processes, this methodology offers a strategic path to success.