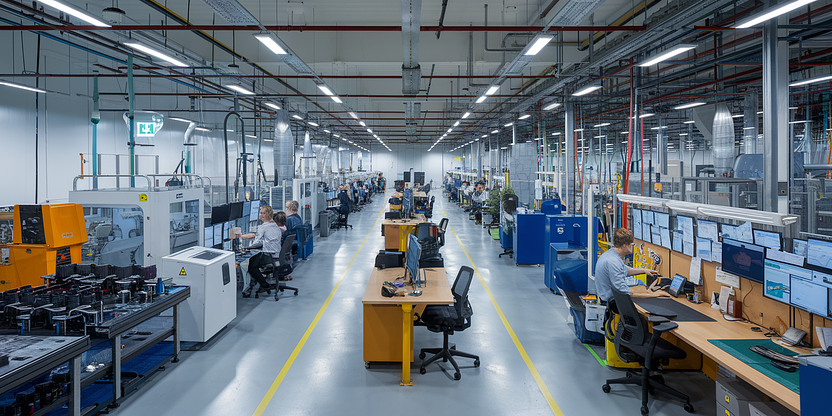
The Complete Checklist for Manufacturing Facility Layout
Designing an efficient manufacturing facility layout is a complex process that significantly affects the productivity, safety, and profitability of an operation. A well-optimized layout can enhance workflow, minimize waste, maximize space utilization, and facilitate better communication and coordination among various departments. As manufacturers face increasing pressures to reduce costs and improve efficiency, laying out the manufacturing facility correctly is more crucial than ever. This article presents a comprehensive guide, with an actual checklist included, to assist in planning an effective manufacturing facility layout.
Introduction to Manufacturing Facility Layout
A manufacturing facility layout considers the arrangement of physical spaces, machinery, and equipment in a plant. It plays a vital role in determining how effectively a manufacturing process will function. The main goals of a well-designed layout are to ensure safety, increase efficiency, improve product quality, and minimize production time.
Different types of layouts can be implemented based on the specific manufacturing needs. These include process layouts, product layouts, fixed-position layouts, and cellular layouts. Each has its advantages and must be selected based on the production process, product type, and volume of production.
Key Considerations in Facility Layout Design
Workflow Efficiency
A seamless flow of materials, information, and personnel within the facility is critical. The layout should be designed to minimize bottlenecks and ensure that materials move smoothly from one stage of production to the next.Space Utilization
Effective use of space can significantly impact the cost-efficiency of operations. The layout should aim to maximize the functional use of space while ensuring that there is enough room for equipment, inventory, and employees.Flexibility and Scalability
With changing market demands, the ability to adapt quickly is essential for survival. A flexible layout allows for changes in production processes or product lines without significant restructuring. Scalability is also crucial to accommodate growth.Safety and Compliance
Ensuring a safe working environment should be a priority. The layout must comply with industry safety standards and regulations to protect employees and equipment from hazards.Technology Integration
As Industry 4.0 becomes more prevalent, integrating technology into the layout—from automated systems to IoT devices—can enhance productivity and facilitate smarter manufacturing processes.
Checklist for Manufacturing Facility Layout
To guide you in designing a productive and efficient layout for your manufacturing facility, the following checklist outlines critical areas and factors to consider.
Facility Layout Checklist
-
Initial Planning
- Define the objectives and goals for the facility layout.
- List key stakeholders and involve them in the planning process.
- Analyze current processes and identify areas for improvement.
- Review industry standards and regulations for compliance.
-
Space and Location
- Conduct a space analysis to determine future requirements.
- Select a location considering access to suppliers, labor, and markets.
- Plan for amenities like break rooms, restrooms, and parking areas.
-
Design Considerations
- Establish clear aisles and pathways for efficient movement.
- Ensure machinery placement minimizes travel distance and time.
- Consider ergonomic design to enhance worker comfort and efficiency.
-
Material Handling and Storage
- Plan for adequate on-site storage and inventory systems.
- Select appropriate types of material handling equipment.
- Design storage areas for quick access and retrieval of materials.
-
System Flexibility
- Incorporate modular and flexible design principles.
- Design for potential expansion and equipment upgrades.
- Ensure easy reconfiguration of assembly lines and workstations.
-
Safety Measures
- Identify and mitigate potential hazards and risks.
- Install safety equipment and emergency response systems.
- Regularly train employees on safety protocols and procedures.
-
Technology and Automation
- Implement automation where feasible to enhance efficiency.
- Ensure data and communication systems are robust and scalable.
- Plan for the integration of smart technology and IoT devices.
-
Environmental Considerations
- Aim for energy-efficient design and operations.
- Consider waste management and recycling programs.
- Assess environmental impact and implement green practices.
Implementing the Layout
Once a layout design is finalized, the next phase is its implementation. This involves construction, equipment installation, and thorough testing to ensure the new layout meets the established goals. Training employees on navigating the new layout and understanding changes is crucial for a smooth transition.
Continuous Evaluation and Improvement
After implementation, it is essential to continuously evaluate the layout's effectiveness and make necessary adjustments. Tools such as simulation software can be used for ongoing analysis and optimization. Regular feedback from employees and performance metrics should guide these iterative improvements.
Conclusion
The design of a manufacturing facility layout is a strategic decision that influences operational efficiency, cost, and quality. By considering various aspects and utilizing a comprehensive checklist, manufacturers can create a layout that aligns with their strategic goals and ensures sustainable growth. With continuous evaluation and adaptation, a well-designed facility can maintain its competitive edge in a fast-evolving industry landscape.