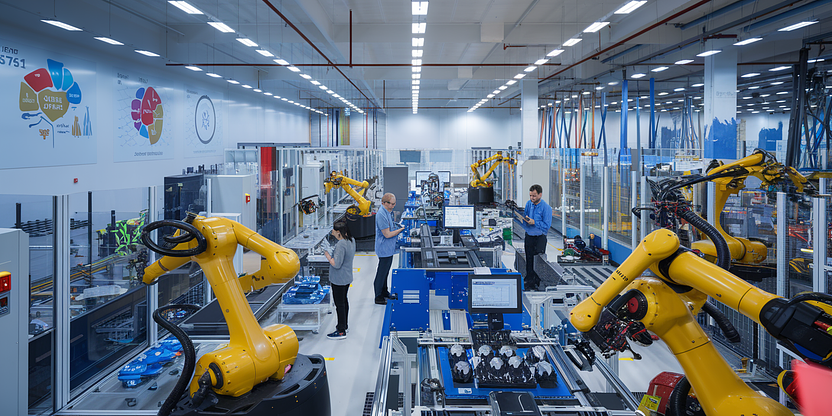
The Complete Checklist for Manufacturing Process Optimization
Streamlining Success: Maximizing Efficiency in the Manufacturing Process
In an era marked by rapid technological advancements and ever-evolving market demands, optimizing the manufacturing process is more critical than ever. By fine-tuning operations, manufacturers not only cut costs but also improve product quality and shorten time-to-market. This results in a stronger competitive edge and better customer satisfaction. This guide delves into the nuances of manufacturing process optimization, providing actionable insights and a comprehensive checklist to streamline operations.
Understanding Manufacturing Process Optimization
Manufacturing process optimization involves the comprehensive assessment and improvement of production procedures to increase efficiency, enhance product quality, ensure worker safety, and reduce environmental impact. It is a multidisciplinary approach that incorporates technological advancements, team collaboration, data analytics, and a continuous improvement mindset.
The primary goals include:
- Maximizing Efficiency: Streamlining operations to reduce waste and downtime.
- Enhancing Quality: Ensuring products meet or exceed industry and customer standards.
- Reducing Costs: Minimizing unnecessary expenses related to production.
- Increasing Flexibility: Adapting quickly to changes in demand or new product lines.
- Ensuring Sustainability: Implementing eco-friendly methods and reducing emissions.
Key Approaches to Process Optimization
Lean Manufacturing: Focuses on minimizing waste without sacrificing productivity by analyzing production flow and eliminating non-value-added activities.
Six Sigma: A data-driven approach aimed at reducing defects and improving quality control through precise measurement and statistical analysis.
Automation and Robotics: Incorporates advanced technology to perform tasks with precision, speed, and consistency, reducing labor costs and human error.
Enterprise Resource Planning (ERP) Systems: Integrates internal and external management information, automating processes to streamline operations and improve decision-making.
Predictive Maintenance: Uses data analytics and IoT (Internet of Things) technologies to predict equipment failures before they occur, reducing downtime and repair costs.
Employee Training and Development: Equips employees with the skills and knowledge to adapt to new technologies and processes, fostering a culture of continuous improvement.
The Manufacturing Process Optimization Checklist
Utilizing a checklist can ensure no aspect of the manufacturing process is overlooked. Here is a comprehensive checklist to guide your optimization efforts:
-
Data Collection and Analysis
- [ ] Gather data on current production processes.
- [ ] Implement analytics tools to interpret this data.
- [ ] Identify trends and areas for potential improvement.
-
Process Evaluation
- [ ] Map out the entire production workflow.
- [ ] Identify bottlenecks and redundancies.
- [ ] Evaluate resource allocation and usage.
-
Lean Techniques Implementation
- [ ] Train staff on lean principles and techniques.
- [ ] Apply 5S (Sort, Set in order, Shine, Standardize, Sustain) methodology.
- [ ] Establish Kaizen (continuous improvement) teams.
-
Quality Control Enhancements
- [ ] Implement Six Sigma or similar quality management systems.
- [ ] Conduct regular quality audits and assessments.
- [ ] Set clear quality benchmarks and metrics.
-
Technology Integration
- [ ] Evaluate the feasibility of automation and robotics.
- [ ] Upgrade to an advanced Manufacturing Execution System (MES).
- [ ] Implement ERP systems to integrate various business processes.
-
Maintenance and Safety Measures
- [ ] Schedule regular maintenance and inspections.
- [ ] Incorporate predictive maintenance technologies.
- [ ] Ensure compliance with safety standards and protocols.
-
Sustainability Initiatives
- [ ] Optimize for energy-efficient practices and equipment.
- [ ] Reduce waste through recycling and material reuse.
- [ ] Invest in renewable energy sources where possible.
-
Workforce Engagement
- [ ] Provide continuous training and development opportunities.
- [ ] Foster open communication and feedback loops.
- [ ] Encourage employee involvement in problem-solving initiatives.
Continuous Improvement and Monitoring
Optimization isn't a one-time endeavor but a continuous cycle. Post-implementation, it's essential to monitor the results and iterate on the strategies employed. Regularly revisiting and updating the approach ensures alignment with the latest industry advancements and shifts in consumer demand.
Leaders should maintain a proactive stance, measuring performance through key performance indicators (KPIs) such as cycle time, overall equipment effectiveness (OEE), defect rates, and energy consumption. Leveraging tools like real-time dashboards and mobile applications allows for timely decision-making and quick responses to any deviation from planned outcomes.
Conclusion
Manufacturing process optimization is an ongoing journey that demands attention to detail, commitment to excellence, and an openness to change. By integrating the checklist provided with modern technologies and methodologies, manufacturers can significantly enhance their operational prowess, delivering superior products while maintaining sustainable practices. Embracing this dynamic approach not only ensures survival in the competitive landscape but sets the stage for long-term success and innovation.