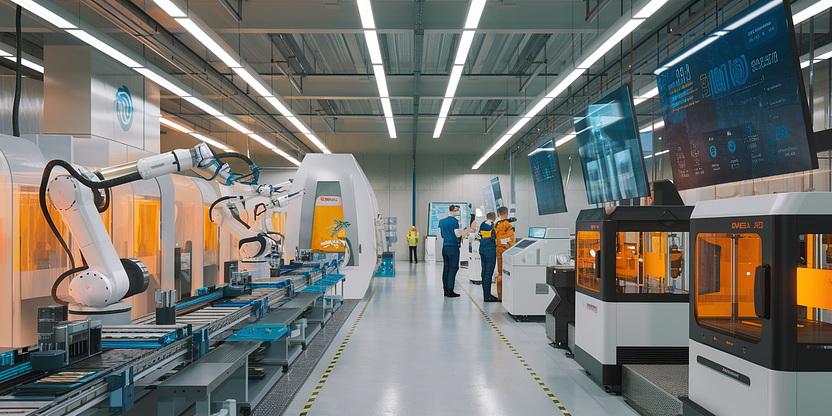
The Complete Checklist for New Manufacturing Technology Adoption
Navigating the Future: Embracing New Manufacturing Technologies
The world of manufacturing is constantly evolving. With the rapid advancement of technologies like Industry 4.0, IoT (Internet of Things), AI (Artificial Intelligence), robotics, additive manufacturing (3D printing), and more, manufacturers are being pushed to streamline operations, reduce costs, and improve productivity. However, adopting new technology can be daunting, given the complexity, cost, and risks involved. This comprehensive guide provides an essential checklist to ensure successful technology adoption for manufacturers, intending to guide businesses through a well-structured process from preparation to implementation and beyond.
Understanding the Need for New Manufacturing Technology
The competitive landscape in manufacturing is intense, driven by consumer demand for high-quality products at lower prices and heightened efficiency expectations. Therefore, adopting new technology is not just about staying relevant; it's about gaining a strategic edge. While the benefits are immense—increased efficiency, improved product quality, and enhanced safety—careful planning is paramount to avoid pitfalls.
Steps for Successful Technology Adoption
-
Assessment and Feasibility Study
- Identify Needs and Goals: Recognize business objectives and what you aim to achieve with new technology. Is the goal to increase production speed, improve quality, or reduce costs?
- Research Technologies: Stay informed about emerging technologies relevant to your industry. Understanding technological trends builds a foundation for making informed decisions.
-
Cost Analysis and Budgeting
- Initial Costs: Consider the immediate expenses, including purchasing, installation, and training.
- Long-Term Costs: Factor in maintenance, downtime, and potential upgrades.
- Calculate ROI: Estimate potential returns on investment, considering both tangible and intangible benefits like improved safety and employee satisfaction.
-
Engaging Stakeholders
- Build a Team: Assemble a cross-functional team from management, operations, IT, and finance to provide diverse insights.
- Communication Plan: Develop a communication plan to keep stakeholders informed and engaged throughout the adoption process.
-
Vendor Selection and Partnerships
- Research Vendors: Evaluate options based on reputation, support services, adaptability, and technology robustness.
- Strategic Partnerships: Consider forming partnerships for better integration and continuous support.
-
Implementation Planning
- Project Management: Use project management methodologies to create an actionable implementation plan.
- Pilot Testing: Run pilot tests to understand the technology's impact on existing processes and make necessary adjustments.
- Staff Training: Invest in comprehensive training programs to ensure employees are well-prepared to work with new technology.
-
Execution and Monitoring
- Deploy Technology: Implement the technology as per the planned phases.
- Monitor Performance: Regularly assess the system performance against predefined metrics and KPIs.
- Feedback Loop: Create channels for receiving feedback from operators and addressing concerns promptly.
-
Continuous Improvement
- Ongoing Evaluation: Continuously measure the impact of the new technology on business outcomes.
- Upgrade Paths: Stay open to future technological improvements and upgrades to prevent obsolescence.
The Complete Checklist for New Manufacturing Technology Adoption
To effectively navigate the landscape of technology adoption, here's a simplified and comprehensive checklist to guide manufacturers through the process:
-
[ ] Identify Core Needs:
- Define specific goals and requirements.
- Align technology with business strategy.
-
[ ] Feasibility and Research:
- Conduct feasibility studies.
- Analyze existing technology trends and options.
-
[ ] Budget Planning:
- Draft a budget that includes both immediate and long-term costs.
- Compare potential ROI against the investment.
-
[ ] Stakeholder Engagement:
- Assemble a multidisciplinary team.
- Develop and execute a communication plan.
-
[ ] Vendor and Partner Selection:
- Evaluate potential vendors and form strategic alliances.
- Focus on reliability and post-sale support.
-
[ ] Implementation Process:
- Establish a project timeline and milestones.
- Conduct pilot testing and refine strategies.
-
[ ] Training and Education:
- Develop user-specific training sessions.
- Collect feedback for improvement.
-
[ ] Deployment and Monitoring:
- Rollout technology as planned.
- Monitor KPIs and address any issues swiftly.
-
[ ] Review and Adaptation:
- Assess the performance and impact on operations.
- Prepare for future technology enhancements.
Embracing the Future
The journey towards embracing new manufacturing technology is both challenging and rewarding. By following this structured process and utilizing the checklist, manufacturers can mitigate risks, enhance productivity, and drive their organizations towards a more innovative and technologically advanced future. Remember, successful technology adoption is not a destination but a continuous journey of adaptation and improvement.
In adopting new manufacturing technologies, it is crucial to maintain flexibility and openness to change as technology and market needs evolve. Keeping abreast of technological advances will not only enhance operational efficiency but will also position your organization as a leader amidst industry competitors who are yet to capitalize on these new-age developments.