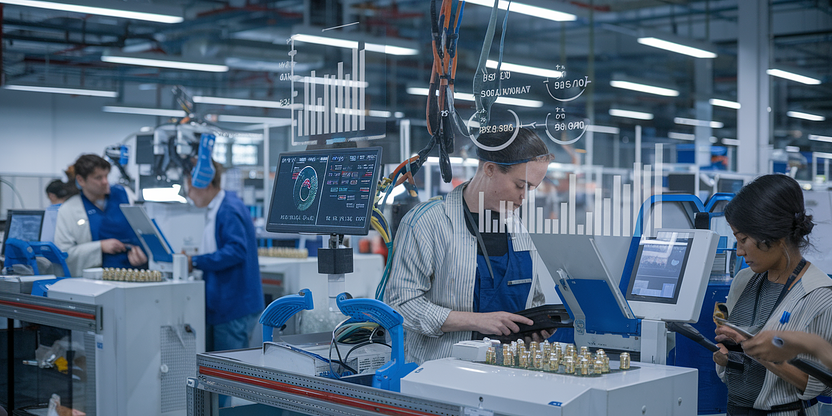
The Complete Checklist for Product Quality Assurance in Manufacturing
Ensuring Excellence: A Comprehensive Guide to Product Quality Assurance in Manufacturing
In today's competitive market, ensuring that your manufacturing process produces high-quality products is crucial not only for customer satisfaction but also for maintaining brand reputation, loyalty, and market share. Product Quality Assurance (QA) encompasses the strategies and methodologies employed to ensure that end products meet the required standards of quality. This article presents an in-depth exploration of QA in manufacturing, along with a comprehensive checklist to guide you through the process efficiently and effectively.
Understanding Quality Assurance in Manufacturing
Quality Assurance refers to the proactive measures taken to ensure that a product or service will satisfy the given requirements for quality. Unlike Quality Control (QC), which focuses on identifying defects in finished products, QA is about preventing defects by revising and optimizing processes, training personnel, and establishing robust systems.
Key Components of Quality Assurance:
- Quality Planning: Establishing objectives and requirements for quality.
- Quality Control: Monitoring specific outcomes to determine if they match desired quality levels.
- Quality Improvement: Continuous evaluation and enhancement of processes and systems.
- Regulatory Compliance: Ensuring adherence to industry standards and regulations.
The Importance of a Comprehensive QA Program
A robust QA program helps in preventing defects, reducing waste, and ensuring that customers receive products that meet or exceed expectations. It also helps in:
- Minimizing costs associated with rework, scrap, and warranty claims.
- Enhancing customer satisfaction and trust.
- Improving operational efficiency and employee morale.
Implementing an Effective QA Strategy
To achieve an effective QA strategy, manufacturers should focus on best practices and implement a structured approach that encompasses various stages, from product design to production and post-production analysis.
Here's a step-by-step guide to developing a successful QA strategy:
- Define Quality Standards and Objectives
Establish clear and measurable quality objectives aligned with customer expectations and regulatory requirements. Quality standards could include ISO certifications or industry-specific benchmarks.
- Develop Process Documentation
Create detailed process documentation, including standard operating procedures (SOPs) and work instructions. Documentation should be consistently updated to reflect any process changes.
- Train and Empower Employees
Conduct regular training programs for employees at all levels. Make sure your team understands quality standards and their role in maintaining them.
- Implement Risk Management
Identify potential risks and develop mitigation strategies to address them effectively. Utilize tools like Failure Mode and Effects Analysis (FMEA) to identify and prioritize potential failure points in the production process.
- Choose the Right Tools and Technologies
Implement advanced technologies like Statistical Process Control (SPC), Six Sigma, and automation tools to monitor and control production processes in real-time.
- Establish a Feedback Loop
Encourage customer feedback and use it to refine processes and improve product quality. Implement a system for tracking and analyzing customer complaints and warranty claims to identify trends and areas for improvement.
- Monitor Supplier Quality
Develop strong supplier relationships and conduct regular audits to ensure materials meet required quality standards. A robust Supplier Quality Management (SQM) program can help mitigate risks from the start.
The Quality Assurance Checklist for Manufacturing
To streamline your QA process, here is a comprehensive checklist that can be customized to fit your specific needs:
- [ ] Establish Quality Objectives: Align quality goals with customer needs and regulatory requirements.
- [ ] Document Processes: Create and maintain SOPs and work instructions.
- [ ] Employee Training: Regularly educate staff on quality standards and procedures.
- [ ] Implement Risk Analysis: Use tools like FMEA to identify potential risks.
- [ ] Utilize Advanced Technologies: Deploy tools like SPC and Six Sigma for process monitoring.
- [ ] Develop Feedback Mechanisms: Collect and analyze customer feedback regularly.
- [ ] Supplier Quality Management: Monitor supplier performance and quality through regular audits.
- [ ] Conduct Regular Audits: Schedule internal and external audits to ensure compliance with quality standards.
- [ ] Continuous Improvement: Encourage a culture of continuous improvement and proactive problem-solving.
Conclusion
A well-implemented Quality Assurance program in manufacturing is crucial for ensuring product excellence and operational efficiency. By following the structured approach and checklist outlined in this article, manufacturers can safeguard product quality, reduce costs, and enhance customer satisfaction. Continuous evaluation and improvement of QA processes will not only meet but anticipate and exceed customer expectations, solidifying a manufacturer’s position in a competitive market.