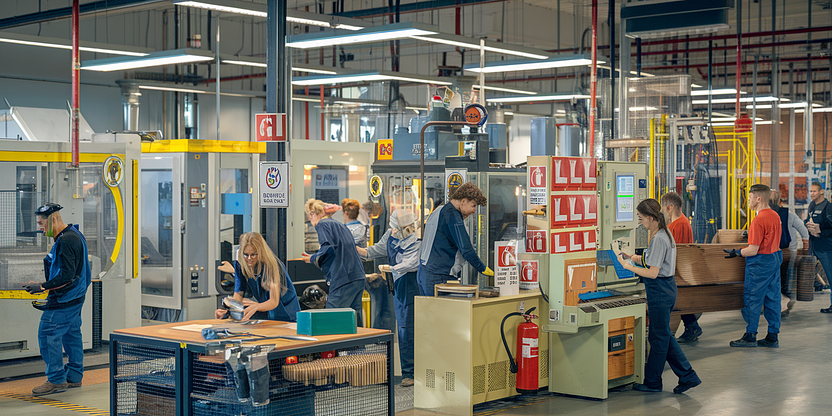
The Complete Checklist for Safety Protocols in Manufacturing
Ensuring Safety in Manufacturing: A Comprehensive Guide
Manufacturing has long served as the backbone of most industrial economies, producing everything from raw materials to complex machinery. While this sector is often a hub of innovation and productivity, it also presents unique hazards. From heavy machinery to hazardous materials, employees face a variety of risks. This article will provide a thorough exploration of safety protocols designed to mitigate these risks, enhancing worker safety and ensuring compliance with legal regulations.
Understanding the Importance of Safety in Manufacturing
Safety protocols in manufacturing environments aren’t just a legal requirement—they are a fundamental aspect of operational efficiency and employee welfare. Implementing robust safety measures can significantly reduce workplace accidents, decrease downtime, and enhance overall productivity. This approach not only safeguards employees but is also economically advantageous for businesses as it reduces potential compensation costs and fines for non-compliance.
Key Areas of Safety in Manufacturing
1. Machinery and Equipment Safety
Machinery in factories often operates under extreme conditions and requires specific safety measures. Regular maintenance, proper training for machinery handling, installation of safety guards, and emergency shutoff systems are critical components. Operators should receive adequate instruction on the safest operational practices and regular updates to safeguard their well-being.
2. Electrical Safety
The diverse array of electrical equipment used in manufacturing presents its own set of risks. Adhering to standards set by organizations like OSHA in the United States can help mitigate these risks. Ensuring that all wiring is up to code, using the appropriate Personal Protective Equipment (PPE), and providing training on handling electrical devices safely are crucial aspects.
3. Hazardous Materials Handling
Many manufacturing processes involve the use of potentially dangerous materials, from chemicals to flammable liquids. Proper labeling, secure storage practices, and detailed handling instructions are essential. Employees must be trained to handle spills and understand the Material Safety Data Sheets (MSDS) associated with these substances.
4. Fire Safety
Fire safety is paramount, given the kind of machinery and materials often present in manufacturing units. This involves the installation of fire detection and suppression systems, regular fire drills, and clear emergency exit routes. Employees should be clearly educated about the locations and usages of fire extinguishers and evacuation plans.
5. Ergonomic Practices
Repetitive tasks and poor ergonomics can lead to musculoskeletal disorders among workers. Implementing ergonomic solutions, such as adjustable workstations or supportive seating, can help mitigate these risks. Regular breaks and training on proper lifting techniques are advisable.
6. Health Monitoring and First Aid
A clear protocol for health monitoring, including periodic health checks and the availability of first aid kits in easily accessible locations, is vital. Qualified individuals should always be on hand to administer first aid, and employees should know how to report injuries correctly.
Comprehensive Safety Protocol Checklist
To ensure no aspect of workplace safety is overlooked, deploying a comprehensive checklist is beneficial. Here’s an example checklist to guide safety protocol implementation in manufacturing:
Safety Protocol Checklist
-
Machinery and Equipment
- [ ] Conduct regular maintenance and safety checks.
- [ ] Install safety guards on machinery.
- [ ] Provide operator training and certification.
-
Electrical Safety
- [ ] Ensure wiring and installations comply with standards.
- [ ] Use appropriate PPE.
- [ ] Provide electrical safety training.
-
Hazardous Materials Handling
- [ ] Label and store materials properly.
- [ ] Train employees on MSDS and spill response.
-
Fire Safety
- [ ] Install fire detection and suppression systems.
- [ ] Conduct regular fire drills.
- [ ] Clearly mark and educate on emergency exits.
-
Ergonomics
- [ ] Implement ergonomic workstations.
- [ ] Educate on proper lifting techniques.
-
Health Monitoring and First Aid
- [ ] Conduct periodic health checks.
- [ ] Provide accessible first aid kits.
- [ ] Train employees in first aid and injury reporting.
Conclusion
Prioritizing safety in the manufacturing industry not only enhances worker protection but also promotes efficiency and compliance with legal obligations. Regularly reviewing and updating safety protocols, employing comprehensive training programs, and adhering to a detailed checklist are essential steps toward creating a safe and productive manufacturing environment. Businesses that champion these safety measures are better equipped to face the challenges of today’s industrial world, ensuring longevity and sustainability in their operational practices.