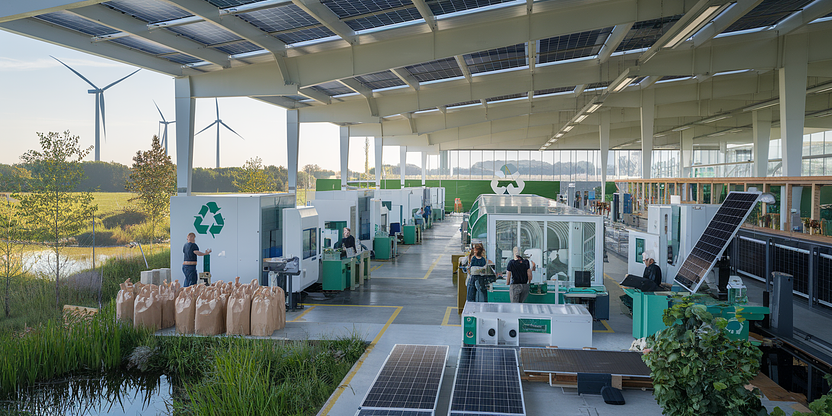
The Complete Checklist for Sustainable Manufacturing Practices
The Comprehensive Guide to Implementing Sustainable Manufacturing Practices
As global industries continue to expand, the urgency of addressing environmental concerns becomes more pressing. Manufacturing processes, in particular, have garnered significant attention due to their substantial ecological footprint. Sustainable manufacturing is an approach that not only reduces environmental impact but also drives innovation, cost-efficiency, and societal benefits. This comprehensive guide provides an in-depth look at how manufacturers can transition towards sustainability.
Understanding Sustainable Manufacturing
Sustainable manufacturing refers to the creation of manufactured products through economically-sound processes that minimize negative environmental impacts while conserving energy and natural resources. It aims to enhance employee, community, and product safety.
The Importance of Sustainable Manufacturing
Environmental Conservation: Reducing waste, emissions, and resource consumption helps preserve ecosystems and biodiversity.
Economic Benefits: Sustainable practices frequently lead to cost savings through waste reduction, improved efficiency, and resource optimization.
Regulatory Compliance: Governments worldwide are implementing stricter regulations to mitigate climate change. Complying proactively with these can prevent potential fines and sanctions.
Market Advantage: Consumers are increasingly preferring eco-friendly brands. Sustainable practices can enhance brand reputation and customer loyalty.
Key Elements of Sustainable Manufacturing
Energy Efficiency: This involves reducing energy consumption and switching to renewable energy sources.
Resource Efficiency: Optimizing the use of raw materials to minimize waste and incorporate recyclables wherever possible.
Waste Management: Implementing systems to reduce, reuse, and recycle waste materials.
Sustainable Product Design: Designing products with minimal environmental impact over their lifecycle.
Pollution Prevention: Implementing processes to reduce emissions and discharges of harmful substances.
Life Cycle Assessment (LCA): Evaluating the environmental impacts associated with all stages of a product's life.
Implementing Sustainable Manufacturing: A Checklist
Integrating sustainable practices into manufacturing operations calls for a structured approach. Here’s a checklist to guide you through the process:
[ ] Conduct an Environmental Impact Assessment: Evaluate current processes to identify areas for improvement.
[ ] Set Clear Sustainability Goals: Define specific, measurable, and time-bound sustainability objectives.
[ ] Invest in Energy-Efficient Technology: Upgrade to machinery and technology that consume less energy.
[ ] Adopt Renewable Energy Sources: Transition to wind, solar, or other renewable energy solutions.
[ ] Minimize Waste Through Lean Manufacturing: Implement lean manufacturing techniques to enhance efficiency.
[ ] Utilize Recycled and Sustainable Materials: Source materials that have been recycled or have the least environmental impact.
[ ] Educate and Train Employees: Foster a culture of sustainability by training employees on best practices.
[ ] Engage Stakeholders: Work with suppliers, customers, and other stakeholders to promote sustainability throughout the supply chain.
[ ] Monitor and Report Progress: Implement systems to track progress and report on sustainability metrics.
[ ] Implement a Pollution Prevention Strategy: Focus on reducing emissions and toxic substances in your operations.
Case Studies of Successful Sustainable Manufacturing
One of the best ways to understand the successful implementation of sustainable practices is by examining real-world examples. Here are a few noteworthy case studies:
1. Interface Inc.: As a global leader in modular flooring, Interface Inc. has spearheaded initiatives such as using recycled materials and developing carbon-neutral products. Their Mission Zero promises to eliminate negative environmental impacts by 2020.
2. Toyota USA: Recognized for its efforts in reducing water usage, waste generation, and energy consumption across manufacturing plants, Toyota has established numerous eco-friendly strategies. For example, the Kentucky plant reduced water usage by utilizing an innovative rainwater recycling system.
3. Unilever: Focused on reducing environmental footprint while increasing positive social impact, Unilever aims to halve its greenhouse gas impact by 2030. The company emphasizes efficient resource use and sustainable sourcing practices.
Future Trends in Sustainable Manufacturing
Looking forward, sustainable manufacturing is poised to be influenced by several key trends:
Circular Economy: Embracing a circular economy model will further drive the reuse and recycling of materials.
Industry 4.0: Smart technologies and IoT can vastly improve efficiencies and sustainability practices.
Green Chemistry: Using chemical products and processes that reduce or eliminate hazardous substances will become more prevalent.
Decarbonization: There will be an increased emphasis on pursuing methods and technologies to significantly reduce carbon emissions.
Conclusion
Transitioning to sustainable manufacturing is not merely a trend but a necessary evolution. By adopting sustainable practices, manufacturers can not only protect our planet but also achieve economic savings and competitive advantages. The journey toward sustainability demands commitment, innovation, and strategic planning. The checklist provided can serve as a guide for companies seeking to make responsible choices that ensure a better future for all.