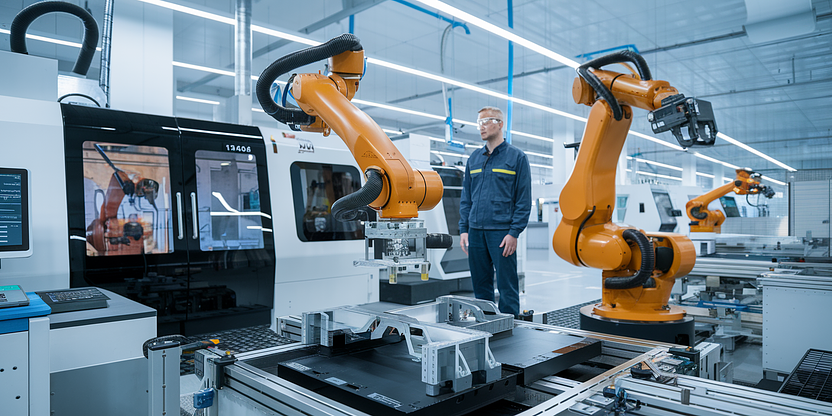
The Complete Checklist for Technology Integration in Manufacturing
As manufacturing landscapes evolve, technology integration emerges as a pivotal factor in maintaining competitiveness and achieving operational excellence. Adopting advanced technologies can significantly enhance manufacturing processes, improve efficiency, reduce costs, and facilitate innovation. This article aims to provide a comprehensive guide for technology integration in manufacturing, offering insights into the types of technologies available, the benefits they provide, and an extensive checklist to ensure successful implementation.
Understanding the Need for Technology Integration
The push for technological advancements in manufacturing is driven by various factors, including global competition, the demand for higher quality and efficiency, and the need for sustainability. As industries face pressure to be more agile and innovative, integrating technologies such as the Internet of Things (IoT), Artificial Intelligence (AI), robotics, and smart data analytics becomes essential.
Key Benefits
Improved Efficiency and Productivity: Automation and interconnected systems streamline production processes, reducing human error and increasing output.
Enhanced Flexibility and Agility: Advanced manufacturing technologies enable quick adaptation to market changes and customer demands.
Cost Reduction: By optimizing operations and reducing waste, technology integration can lead to significant cost savings.
Quality Assurance: Real-time data and machine learning can detect defects, ensuring high standards and minimizing recalls.
Sustainability: Energy-efficient technologies and optimized resource use contribute to environmental sustainability.
Types of Technologies in Manufacturing
Industrial Internet of Things (IIoT): Devices connected across the manufacturing floor collect and analyze data, providing insights for optimization.
Artificial Intelligence and Machine Learning: They enhance decision-making through predictive maintenance, demand forecasting, and quality control.
Robotics and Automation: From robot arms to automated conveyor belts, they streamline repetitive tasks, reducing labor costs.
Additive Manufacturing: Also known as 3D printing, it boosts prototyping and small-batch production capabilities.
Advanced Data Analytics: Big data tools analyze massive datasets to uncover patterns and inform strategic decisions.
Cybersecurity Solutions: With increasing cyber threats, robust cybersecurity measures protect sensitive data and systems.
The Checklist for Technology Integration in Manufacturing
Before diving into technology integration, it is crucial to plan meticulously to avoid common pitfalls. Below is a complete checklist to guide you through the process:
Initial Assessment
- Evaluate Current Processes: Conduct a thorough analysis of current manufacturing processes to identify pain points and areas for improvement.
- Set Clear Objectives: Define what you aim to achieve with technology integration, such as reduced costs, increased efficiency, or enhanced sustainability.
- Budget Planning: Establish a realistic budget considering both initial costs and long-term benefits. Don’t forget to include training and maintenance expenses.
Selecting Technologies
- Research Latest Innovations: Stay updated on the latest advancements in manufacturing technology.
- Vendor Assessment: Choose reliable technology vendors with proven track records in your industry.
- Compatibility Check: Ensure the selected technology can integrate seamlessly with existing systems.
Implementation
- Pilot Test: Start with a small-scale pilot to assess feasibility and fine-tune processes.
- Employee Training: Implement comprehensive training programs to equip the workforce with necessary skills to handle new technologies.
- Change Management: Develop a change management strategy to facilitate smooth transition and minimize resistance.
Monitoring and Optimization
- Performance Metrics: Set key performance indicators (KPIs) to evaluate the success of the integration.
- Feedback Loop: Establish processes for continuous feedback and improvement from workforce and stakeholders.
- Regular Audits: Conduct regular audits to identify any issues and ensure technologies are delivering expected benefits.
Cybersecurity Measures
- Data Protection: Implement strict data protection laws and encryption protocols.
- Access Control: Manage access to sensitive information through robust authentication measures.
- Incident Response Plan: Develop a comprehensive incident response plan to handle potential security breaches.
Overcoming Challenges
Integrating technology into manufacturing comes with its challenges. These may include high initial investments, resistance from employees, and potential disruptions during implementation. To mitigate such challenges, management should prioritize clear communication, provide ample training, and engage employees throughout the transition process.
Conclusion
The journey to integrating technology in manufacturing is complex but rewarding. By following the comprehensive checklist outlined above, manufacturers can strategically navigate the complexities of technology integration and chart a path towards enhanced productivity, efficiency, and innovation. With a clear vision and methodical planning, the benefits of technological advancements can be fully realized, positioning manufacturing firms for sustained growth in a technology-driven world.
Embracing technology integration is not merely about keeping up with trends; it's about fostering an environment where innovation thrives and propels the industry into a more advanced, efficient, and sustainable future.