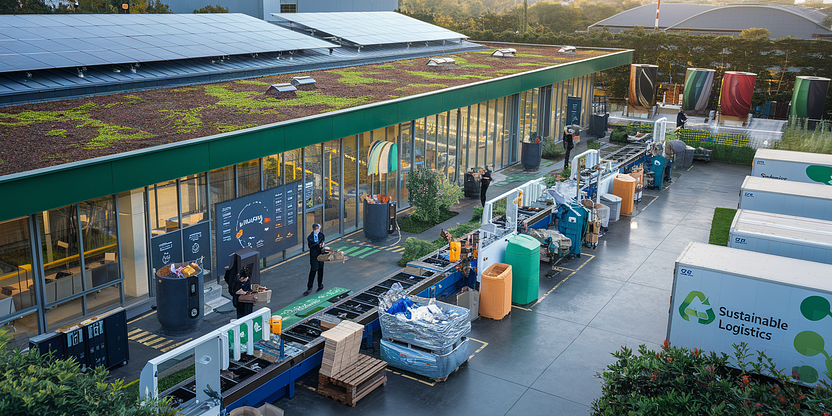
The Complete Checklist for Waste Minimization in Manufacturing
Maximizing Sustainability: A Comprehensive Guide for Minimizing Waste in Manufacturing
In today's fast-paced industrial landscape, achieving sustainability is not just an ethical consideration but a business imperative. Waste minimization in manufacturing is an essential component of sustainable practices. It can lead to significant cost savings, improved efficiency, and a reduced environmental footprint. This comprehensive guide delves into effective waste minimization strategies for manufacturing enterprises, offering actionable insights to foster green and efficient production processes.
Understanding the Importance of Waste Minimization
Waste minimization in manufacturing is pivotal for several reasons:
Environmental Impact: Reducing waste helps decrease pollution and conserves natural resources, contributing to environmental enhancement and sustainability.
Cost Efficiency: Less waste means lower disposal costs and more efficient use of materials, leading to substantial cost savings for manufacturers.
Regulatory Compliance: Complying with environmental standards and regulations often involves managing waste effectively. Failing to do so can result in hefty fines and legal issues.
Brand Reputation: Companies recognized for environmental stewardship often enjoy better customer loyalty and enhanced brand image.
Key Strategies for Waste Minimization
Lean Manufacturing: This approach focuses on minimizing waste without sacrificing productivity. Techniques such as Just-In-Time (JIT) production, continuous improvement (Kaizen), and value stream mapping are employed to enhance efficiency.
Material Optimization: Efficient use of raw materials is crucial. This can involve redesigning products to require less material, using recycled materials, or improving inventory management to reduce excess.
Process Modification: Adjusting manufacturing processes to be more efficient can minimize waste. This might involve upgrading technology, optimizing workflows, or redesigning processes.
Employee Training and Engagement: Employees play a key role in waste minimization. Training them to identify waste and implement reduction strategies can have a significant impact.
Waste Segregation and Recycling: Implementing systems to segregate and recycle materials such as paper, plastic, metals, and more within the manufacturing facility can drastically reduce waste sent to landfills.
Supply Chain Collaboration: Working with suppliers to reduce packaging waste, streamline logistics, and implement returnable packaging systems can contribute to overall waste reduction.
Energy Efficiency: Reducing energy waste through efficient lighting, machinery, and building design can significantly decrease environmental impacts and costs.
Lifecycle Analysis: Assessing the entire lifecycle of products, from raw material extraction to disposal, can provide insights into areas for waste reduction.
The Waste Minimization Checklist
To assist manufacturing facilities in systematically approaching waste minimization, here’s a practical checklist:
-
Assess Current Waste:
- Conduct a waste audit to understand current waste streams and volumes.
- Identify the main sources of waste in production processes.
-
Set Reduction Targets:
- Establish clear, measurable goals for waste reduction.
- Prioritize areas with the highest waste levels for immediate action.
-
Engage Employees:
- Develop training programs on waste management and minimization.
- Encourage employee suggestions for improving waste practices.
-
Optimize Materials and Resources:
- Implement material-efficient design practices in product development.
- Utilize recycled or reused inputs for production.
-
Improve Process Efficiency:
- Regularly review and optimize manufacturing processes.
- Invest in technology that reduces waste generation.
-
Implement Recycling Programs:
- Develop a systematic approach for waste segregation and recycling.
- Partner with recycling firms for specific materials not handled in-house.
-
Enhance Supplier Collaboration:
- Work with suppliers to reduce packaging and encourage sustainable practices.
- Negotiate take-back agreements for packaging materials.
-
Review Energy Use:
- Conduct energy audits to identify inefficiencies.
- Implement energy conservation measures and invest in renewable energy sources where feasible.
-
Monitor and Report Progress:
- Regularly track waste reduction metrics and evaluate against targets.
- Communicate progress and improvements to stakeholders.
Implementing Continuous Improvement
Waste minimization is an ongoing process that requires continuous monitoring and improvement. Regular audits and adapting new technologies and methods are crucial for staying ahead of evolving sustainability standards. Implementing a loop of Plan-Do-Check-Act (PDCA) can help maintain momentum and ensure persistent focus on waste reduction.
Conclusion
The manufacturing sector is at a transformative crossroads where embracing waste minimization is not only environmentally prudent but economically beneficial. By integrating the strategies outlined in this guide and adhering to the comprehensive checklist, manufacturers can take substantial steps toward more sustainable operations. This not only safeguards the environment but also fortifies the long-term viability and resilience of manufacturing businesses.