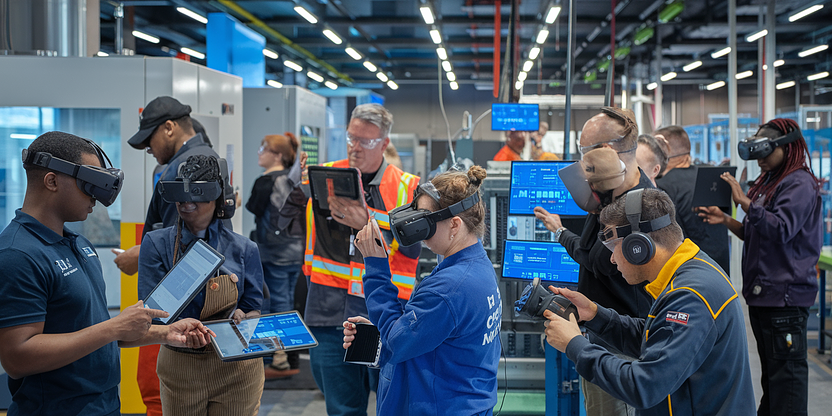
The Complete Checklist for Workforce Training in Manufacturing
Workforce training in manufacturing is a critical component in optimizing operational efficiency, maintaining safety standards, and fostering innovation. As technology advances and production processes become more complex, it is essential for manufacturing companies to ensure their staff is well-trained and capable of adapting to new roles, equipment, and methodologies. An effective workforce training program not only equips employees with necessary skills but also contributes to the overall success of a manufacturing enterprise.
Understanding the Importance of Workforce Training in Manufacturing
In the manufacturing sector, the stakes are high. With global competition and the rapid pace of technological advancement, manufacturers need to be agile and forward-thinking. Effective workforce training addresses several key objectives:
- Increasing Production Efficiency: Trained employees can perform tasks more accurately and efficiently, reducing downtime and waste.
- Enhancing Safety: With adequate training, the workforce is better equipped to handle machinery safely, thereby reducing the risk of accidents and injuries.
- Boosting Employee Morale: Investing in employee training shows a company’s commitment to their personal growth, leading to higher job satisfaction and reduced turnover.
- Ensuring Compliance: Proper training helps ensure compliance with industry regulations and standards, avoiding potential fines and legal issues.
- Promoting Innovation: A well-trained workforce is more capable of contributing to problem-solving and process improvements, driving innovation.
Key Components of Effective Workforce Training
A comprehensive training program should be structured, strategic, and tailored to the unique needs of a manufacturing facility. Here are the critical components that should be incorporated:
- Needs Assessment: Evaluate what skills and knowledge gaps exist within your workforce.
- Training Objectives: Set clear, measurable goals to guide the development and implementation of your training program.
- Curriculum Development: Design training materials that are relevant and engaging, utilizing a mix of theoretical instruction and practical application.
- Technology Integration: Incorporate modern technology such as e-learning platforms, VR simulations, and digital tools to enhance learning experiences.
- Training Delivery: Choose the appropriate delivery method, whether it's instructor-led workshops, online modules, or on-the-job training.
- Evaluation and Feedback: Create mechanisms to assess the effectiveness of training programs and gather feedback to make necessary improvements.
- Continuous Improvement: Training should be an ongoing process, with regular updates and revisions to keep pace with industry changes.
The Ultimate Checklist for Workforce Training in Manufacturing
Here is a practical checklist to ensure your workforce training program is comprehensive and effective:
- [ ] Conduct a thorough skills gap analysis to identify training needs.
- [ ] Develop clear training goals aligned with business objectives.
- [ ] Design a curriculum that includes a balance of theory and hands-on experience.
- [ ] Utilize a mix of training methods, including e-learning and in-person sessions.
- [ ] Regularly update training materials to reflect the latest industry standards and technologies.
- [ ] Implement training on workplace safety and regulatory compliance.
- [ ] Use performance metrics to evaluate training effectiveness.
- [ ] Gather employee feedback to refine training programs continually.
- [ ] Provide opportunities for advanced and specialized training.
- [ ] Establish mentorship programs for knowledge transfer and skills development.
- [ ] Integrate soft skills training to enhance communication, problem-solving, and teamwork.
- [ ] Ensure management support and buy-in for training initiatives.
- [ ] Allocate adequate resources, including time, budget, and personnel, for training.
- [ ] Monitor and review the long-term impact of training on business performance.
Overcoming Common Challenges
Implementing an effective workforce training program in manufacturing can be challenging due to various factors including budget constraints, resistance to change, and time limitations. Strategies to overcome these challenges include:
- Securing Leadership Buy-In: Demonstrating the ROI of workforce training can help secure commitment from leadership.
- Customization: Tailoring training programs to specific job roles and individual learning styles can improve engagement and effectiveness.
- Phased Implementation: Rolling out training programs in phases or pilot groups can ease the transition and provide opportunities for refinement before full-scale deployment.
Conclusion
Manufacturing companies that prioritize workforce training stand to gain a competitive advantage in an increasingly complex and demanding industry landscape. By following a structured checklist and focusing on continuous improvement, manufacturers can ensure their workforce is skilled, compliant, and motivated. The adoption of innovative training solutions and technologies will further support the development of a resilient and empowered workforce, capable of driving the future of manufacturing.